Freyssinet carried out post-tensioning design on Damac Tower, a new high-rise development in London’s Nine Elm
Damac Tower – Post-tensioning design for a new high-rise development in London’s Nine Elm
Client – DAMAC (Nine Elms Property Limited)
Main Contractor – Multiplex Ltd
Structural Engineer – WSP – Parsons Brinkerhoff
Architect – Kohn Pedersen Fox Associates
Frame Contractor – Byrnes Bros Ltd
Post-tensioning Contractor– Freyssinet Ltd
The project
Damac Tower is a circa £240 million residential development consisting of a 50-storey North Tower and a 24-storey South Tower, situated in Nine Elms on the South Bank in London, at the forefront of a multi-billion pound investment that is transforming the area.
The North Tower features interiors by Versace Home and provides 360 residential units, five storeys of office space with a connecting sky bridge to the South Tower, which is topped by an extensive roof garden at level 23. The apartments will offer panoramic views of the city.
The initial concept design by Project Engineer WSP was based on a proposal of post-tensioned slabs to many of the superstructure levels. The central cores form the overall stability system for the building. Wind loads acting on the building are transferred to the floor slabs from the curtain walling via the cladding brackets and the concrete floor slabs act as stiff diaphragms to transfer the wind loads to the cores.
Utilising post-tension design allows for thinner slabs, reducing the weight of the structure into the foundations while still controlling deflections. It also gives the potential to reduce the height of the building, therefore allowing savings on cladding, which in turn may assist with foundation design.
Following intensive development through the tender stages, Freyssinet was commissioned by the frame contractor Byrne Bros to provide the design, supply and installation of post-tensioned slabs and the additional design and detailing of the traditionally reinforced horizontal elements.
The typical floor plates to both towers are 200thk with an average of 4.8kg/m2 of PT and 13kg/m2 of traditional rebar, resulting in an overall of 196 tonnes of post-tensioning and 630 tonnes of associated traditional rebar. The total floor area of the post-tensioned slabs is approx. 44,600 m2 in 72 individual concrete pours.
After the PT system had been installed and checked, a line was sprayed on the deck so that when the deck was removed a tracer is left on the soffit of the slab to indicate the as-built location of tendons.
The post-tensioning system
The slabs were post-tensioned using the Freyssinet 4B13 bonded flat-slab system, with tendons spaced at an average 1.2M centres in each direction.
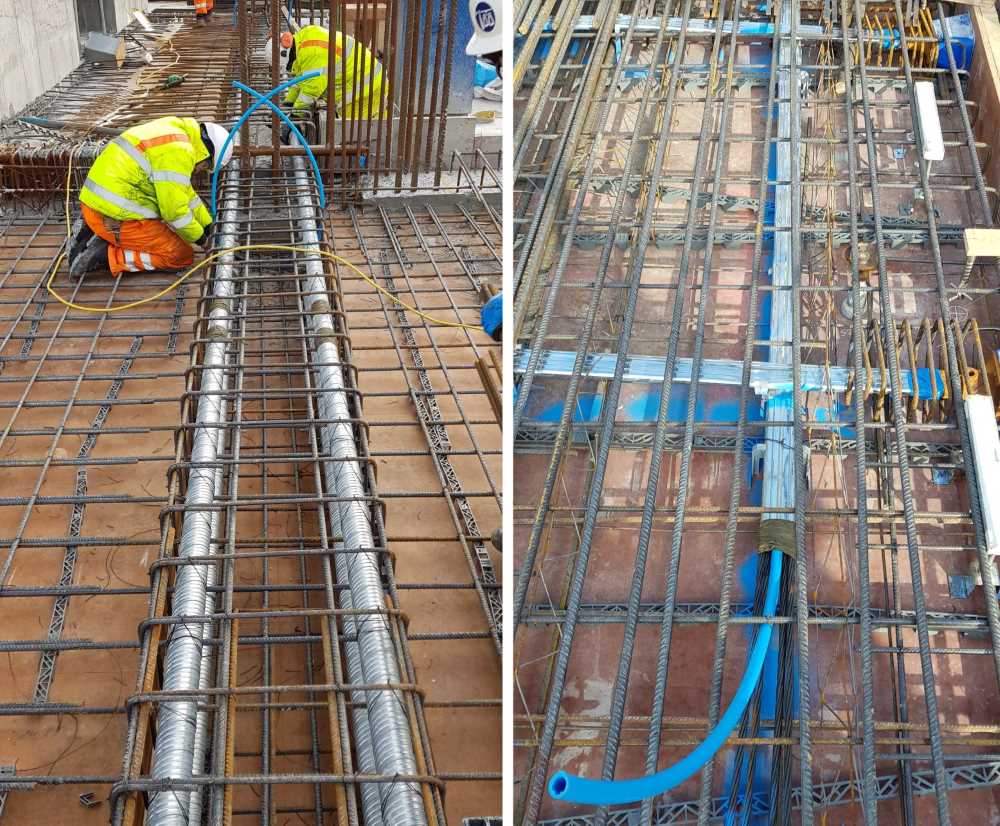
Left: Installation of Freyssibar. Right: Co-ordination of tendon live and dead end with cast-in inserts
As part of the detail design process, Freyssinet ensured co-ordination between cast-in inserts and tendon anchors to minimise potential clashes during installation on site. This coordination also included needle positions for the climbing protective screen.
Whilst loading information, deflection limits and movement and tolerance specification were provided by the project engineers, was vital that the Freyssinet design team also took into account temporary construction loads, as these were higher than those for the service case.
Design criteria
The design criteria is in line with BS EN 1992-1-1(1), BS EN 1992-1-2(2) and Concrete Society Technical Report 43(3). TR 43(2nd Edition) Post tensioned concrete floors: Design Handbook (1994)
Deflection
The suspended floors supporting cladding have been designed to achieve maximum deflections as follows.
- The total long-term deflection due to all permanent and variable loads will be limited to the lesser of span/250 or 25mm.
- The deflection due to variable loads will be limited to the lesser of span/600 or 10mm.
- The deflection due to superimposed permanent and variable loads applied after cladding installation will be limited to 12mm.
- The total differential deflection between adjacent floors after the installation of the cladding will be limited to the lesser of span/500 or 12mm.
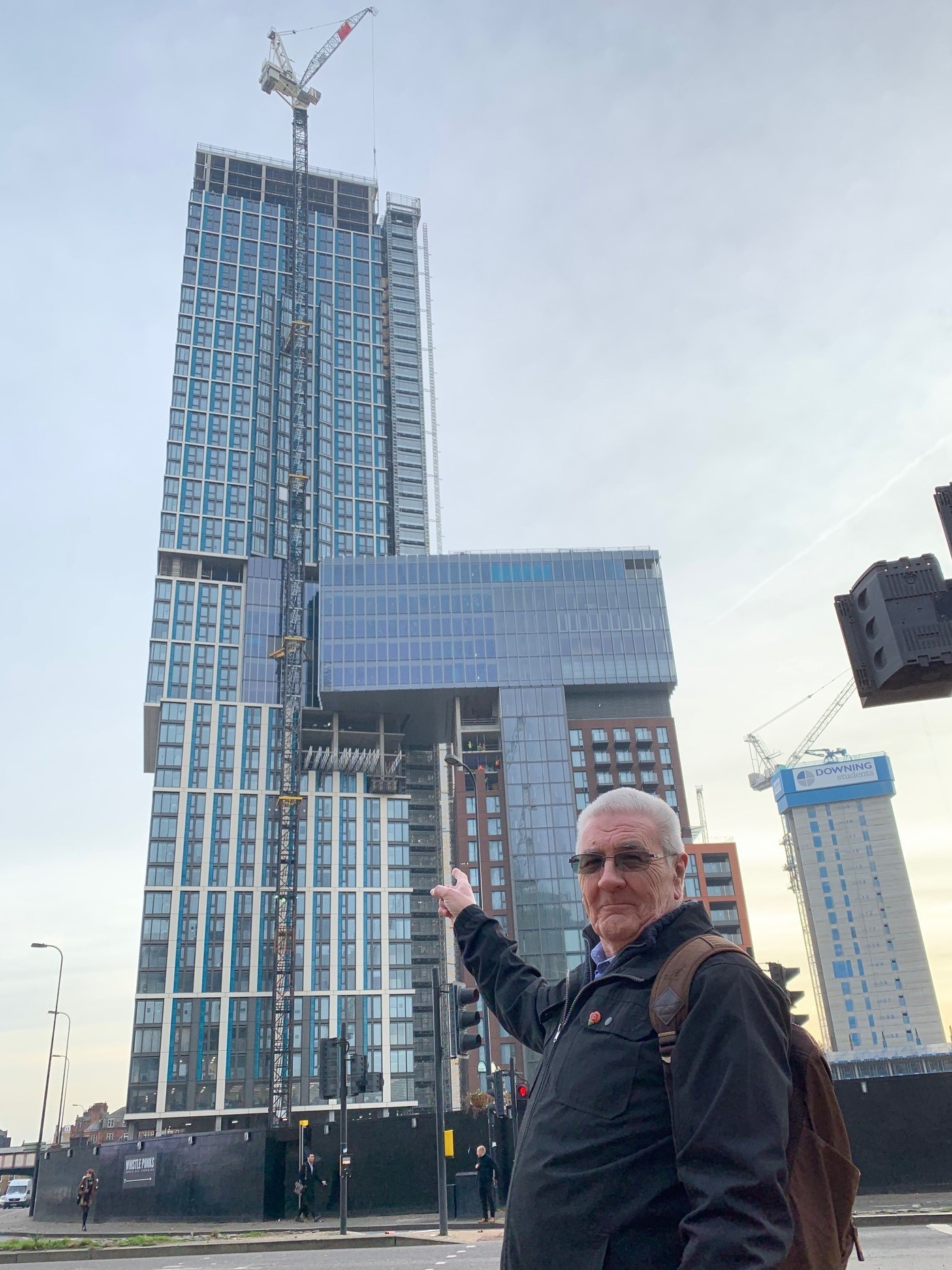
Freyssinet Sales Manager Ron Wilkinson outside Damac Towers
Loadings
- Typical slab loadings: SDL=2.0kN/m2; LL=1.5kN/m2; Cladding=4.8kN/m run
- Tie load at multiple levels caused by walking columns.
Consideration of temporary construction loads
- Wet concrete
- Canti-decks
- Crane ties
- Hoist ties
- Climbing Edge Protection
As part of the design process, consideration had to be given to the tie forces resulting from the walking columns. Freyssinet’s solution was to add extra reinforcement/tendons and Freyssibar.
The super structure was completed in November 2019. The Freyssinet team were highly praised for their work ethic and commitment to the project by the Frame Contractor and Main Contractor.