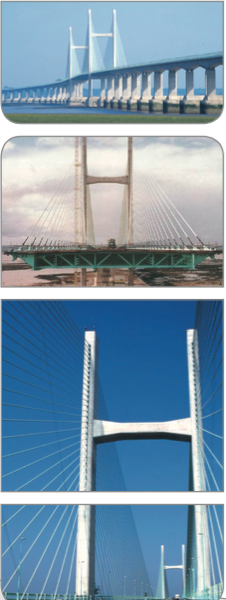
Severn River Crossing Plc
Architect
Percy Thomas Partnership
Structural Engineers
Halcrow – SEEE
Principal Contractor
Laing – GTM JV
Stay Cables, Post Tensioning, Lifting
Freyssinet Ltd
Completion
June 1996
Value
£7m
The Second Severn Bridge crosses the Severn estuary some three miles downstream from the existing suspension bridge. The new bridge will accommodate increasing levels of traffic between England and Wales. The crossing, 5,125 m long, consists of a cable-stayed bridge – central span 456 m long – and two access viaducts. A high tidal range, up to 12.30 m, led the contractor Laing – GTM to use large-scale prefabrication.
The approach viaducts are built from prefabricated segments, installed using a launching girder. The cable-stayed main span is a composite steel-concrete deck built from segments 34.6 m wide and 7 m long, also prefabricated on site. The segments were shifted and lifted using two huge mobile derricks. Foundations and piers were also prefabricated to a large extent: each pylon foundation consists of a reinforced concrete caisson weighing up to 2,000 tonnes. Pier shafts are made of elements with match cast joints, assembled together using vertical prestressing.
The pylons are 150 m high. A lower transverse beam, 40 m above highest tide level, carries the cable-stayed deck. An upper beam, completing a portal frame, is located at mid-height of the stay cable anchoring zone, 110 m above highest tide. Freyssinet post-tensioned the upper beam with 37K15 tendons. Additionally Freyssinet tensioned all the Macalloy bars used in the pylons.
The stay cable system consists of four planes of sixty stay cables, Freyssinet 19 to 75T15, 35 to 243 m long. The stay cables are anchored to the deck via bearing plates and dual-web steel beams. The vertical component of the tensile forces is withstood by transverse brackets protruding from the deck, the horizontal component is transmitted to the deck by shear and compression. The stay cables installed by Freyssinet are galvanised strands, inserted into an HDPE sheath. The strands were tensioned one after the other from deck level using the Freyssinet Isotension system, which is lightweight and manoeuvrable. The casing / anchorage / sheath assemblies are fi lied with petroleum wax. The HDPE sheath has been wrapped with light green adhesive tape.
Freyssinet also undertook various heavy lift operations.
Freyssinet Ltd. Innovation House, Euston Way, Town Centre, Telford, Shropshire, TF3 4LT Phone +44 (0) 1952 201901 Fax +44 (0) 1952 201753 Email info@freyssinet.co.uk